A General Introduction To Microfluidics And Lab On A Chip Devices
Defining microfluidics
The field of microfluidics studies the behavior of fluids flowing through micro-channels, while microminiaturization is concerned with producing devices containing chambers or tunnels that permit fluids to flow through. Essentially, microfluidics is the study of very small volumes of fluids. The smallest unit is the femtoliter (fL), which is a quadrillionth of a liter.
Scientists have built new experiments and inventions based on the unique properties of fluids on the microscopic scale. In microfluidics, an important concept is to integrate operations commonly carried out in a large laboratory into a simple small system. The use of microfluidics in biological analysis is becoming increasingly common today, as it provides efficient tools for multiple research areas:
- Continuous Flow microfluidics
- Digital microfluidics
- Optofluidics
- Acoustofluidics
- Electrophoresis
- Microfabrication.
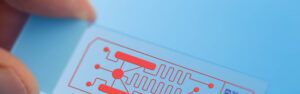
Chips with microfluidic technology
Microfluidic chips are made up of a grid of microchannels that may be molded or etched. Microchannels are interconnected with holes hollowed out through the microfluidic chip to provide a link between the microfluidic chip and the macro-environment. Microfluidic chips facilitate the injection of fluids into and evacuation of fluids from them via these pathways. Fluids can be directed, mixed, separated, or manipulated as part of multiplexing, automation, and high-throughput systems. Precise design of the microchannels network is important to realize desired features (lab-on-a-chip, detection of pathogens, electrophoresis, DNA analysis, etc.). Fluid management systems are essential for accurate fluid control inside microchannels.
What is Lab on Chip?
Science and techniques involved in microfluidics encompass flow management at the micro-scale. With such dimensions, fluids’ dynamics are radically different from the ones usually encountered in daily life. For example, water streams are laminar, meaning they do not mix or form vortices or eddies. The microfluidic revolution in science is based on these and other unique features. For controlling and containing fluids at the microscale, microfluidic chips are utilized. A microchannel pattern is either molded or engraved into these devices. To ensure precise fluid management, active and passive flow control elements, such as membranes or valves, can also be implemented on the chip. Microfluidic chips, then, enable the integration of several functions that would normally require an entire laboratory into a single microfabricated device. Because of this, microfluidics and microfluidic chips are commonly referred to as “Laboratory-on-Chip”.
Lab-On-A-Chip Advantages
There are several advantages of microfluidics: faster reaction times, improved analytical sensitivity, accurate temperature control, portability, easy automation and parallelization, integration of lab routines in one device (lab-on-a-chip). Microfluidic chips can either have these components embedded in them like Quake valves, or they can be external, like pressure controllers. At a microscale, microfluidic devices make use of liquids and gases’ physical and chemical properties. The advantages of microfluidic devices are numerous. The use of microfluidics reduces the amount of chemicals, reagents, and sample volumes used for an analysis, reducing the overall application costs.
The small size of these devices allows them to perform many operations simultaneously, thereby speeding up the experimentation process. Additionally, they offer a high level of data quality and significant parameter control, meaning that you can automate processes while still maintaining performance. It is also capable of analyzing samples with only a very little amount of sample handling.
 As a result of the integrated automation, the microfluidic chip provides the possibility of generating multi-step reactions with low expertise requirements and many features. From detecting toxins to analyzing DNA sequences or creating inkjet printing devices, the microsystems can do it all. For more information about microfluidic applications, visit our dedicated review here. (Application Page)
Microfluidic chips materials
In the past, microfluidic devices have been manufactured with a variety of materials, including glass, silicon, hydrogels and polymers. They fall into three categories: inorganic, polymeric, and paper. Since every material employed in microfluidics has some advantages and drawbacks, there is no such thing as the “perfect” material. Researchers select materials according to their intended applications. A brief review of the most popular materials used in microfluidics will appear in this section.
Microfluidics using silicon
In the fabrication of microfluidic devices, silicon became one of the first materials chosen. Silicon is less utilized today as it is less cost-effective and its opacity renders optical detection unreachable, apart from infrared. Furthermore, a microfabrication facility and clean room are necessary. Even so, it allows high precision silicon machining. Microfluidic chip fabrication can be achieved with silicon due to it being stable, chemically compatible, and electrically conductive; however, this makes it unsuitable for microfluidic applications that require a high voltage, like electrophoresis.
Glass used in microfluidics
In the early days of microfluidic chip manufacturing, glass was also used. This material shares many of the same properties of silicon, including surface stability, thermal conductivity, and solvent compatibility. Aside from its biocompatibility and chemical inertness, glass also has a hydrophilic surface so it can be coated effectively. Several applications require its superior optical transparency, high-pressure resistance, and surface chemistry. Glass is very expensive, which is the main disadvantage of glass microfluidic chips.
Microfluidics with polymers
As a result of their robustness, cost-effectiveness, and strong bio-chemical properties, polymers are widely used to manufacture microfluidic devices. The wide range of polymer materials and the possibility to modify them chemically have made polymers useful in microfluidic devices.
Microfluidic devices can be manufactured rapidly using polymers. Thermoplastics and thermosets are two types. Polystyrene (PS), Polyether Ether Ketone (PEEK), polyethylene terephthalate (PET), polyvinyl chloride (PVC), polymethylmethacrylate (PMMA), polycarbonate (PC), polyetherimide (PEI) and polydimethylsiloxane (PDMS) are thermoplastic polymers that can be used in the fabrication of microfluidic chips.
Hydrogel used in microfluidics
Hydrogel can be molded into different shapes and sizes, and its suppleness enables diverse features to be molded onto it. A safe, cost-effective, commercially available, non-toxic, and biodegradable hydrogel. Hydrogel permits diffusion of cell nutrients and growth factors. Many solutes in agarose gels, a common hydrogel used for microfluidic chips, have remarkably similar diffusion properties to water.
Chips based on paper for microfluidics
The use of paper as a microfluidic chip surface is extremely cheap and promising. Indeed, paper is slender, easy to stock, employ and transport. Chemically, it can bond with molecules or proteins. It is compatible with biological samples. Furthermore, the paper used for microfluidic chips is highly environmentally friendly. Microfluidic devices based on paper have the major disadvantage of being difficult to pattern channels on.