Semiconductor Wafer Polishing
Chemical Mechanical Wafer Polishing is a process that uses a combination of chemicals and mechanical polishing to remove material from the surface of a semiconductor wafer. The chemical component of CMP reacts with the surface being polished, while the mechanical component removes material through physical abrasion. CMP is a highly controlled process, and variations in the composition of the chemical solution and the type of polishing pad can result in different rates of material removal. In addition, CPA can be used to clean semiconductor surfaces by removing particles that could otherwise cause defects in the finished product.
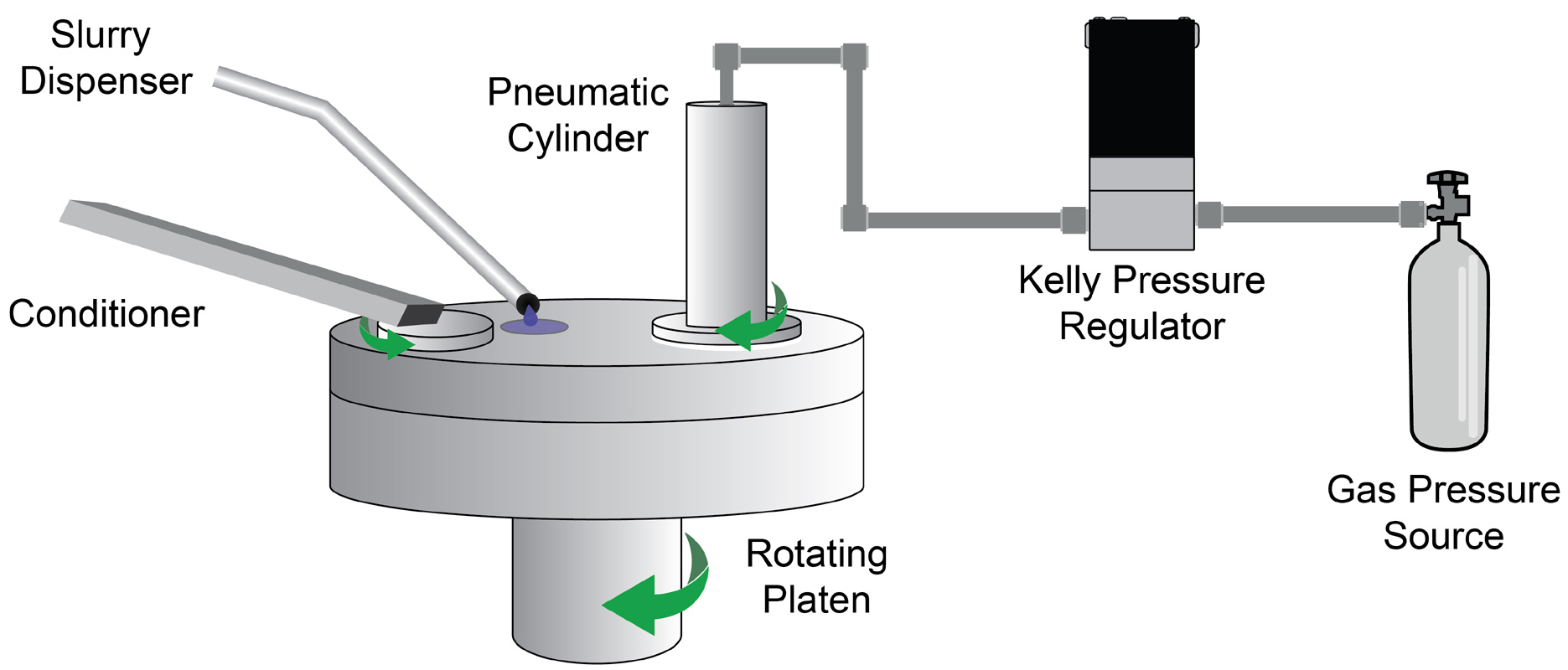
Using the Kelly Electronic Pressure Regulator In The CMP Process
The Kelly Low Flow Regulator is an excellent solution for using precision pressure control to pilot operate the pressure applied to the wafer during the polishing process. Since the regulator is electronically controlled, it can be programmed dynamically by a control system, such as a PLC. This means it can be customized to accurately vary the pressure applied depending on the particular wafer being polished. This provides software engineers the option to preset the regulator to the required pad pressure per CMP sequence. Also, since the pressure regulator is closed-loop controlled, the pressure applied to the polishing pad is maintained even during changes to the downstream pressure, meaning manual adjustment is not necessary.
The regulator also has a feedback signal (analog voltage) representing the current downstream pressure, which can be recorded during the CMP process. This allows for real-time logging of the actual pressures applied through the entire operation, which can be read from the feedback signal into the controller via an ADC (Analog-to-digital converter) and reviewed at a later time. Logging actual CMP pressures applied during the polishing process can provide much-needed traceability for large-scale CMP operations.