Semiconductor Wafer Dicing
Semiconductor wafer cutting, also known as wafer dicing, is a key process in the fabrication of semiconductor devices. It is the stage in which individual semiconductor chips are precisely cut from a silicon wafer, preparing them for eventual assembly into products that power our digital world. As demand for high-performance and miniaturized devices continues to grow, the importance of precision in wafer cutting cannot be understated.
This precision is predicated on the utilization of vacuum pressure, crucial for enabling the exact type of cut necessary for the wafer chuck feature. The wafer chuck is a critical component in many semiconductor manufacturing processes as it holds the wafer in place during the cutting process. For this, an even and stable vacuum pressure is necessary to prevent any shift or movement of the wafer, ensuring the precision of the cutting process.
Enter electronic pressure regulators (EPRs). These devices play a vital role in maintaining this necessary vacuum pressure, and thus are central to the precision and reliability of wafer dicing.
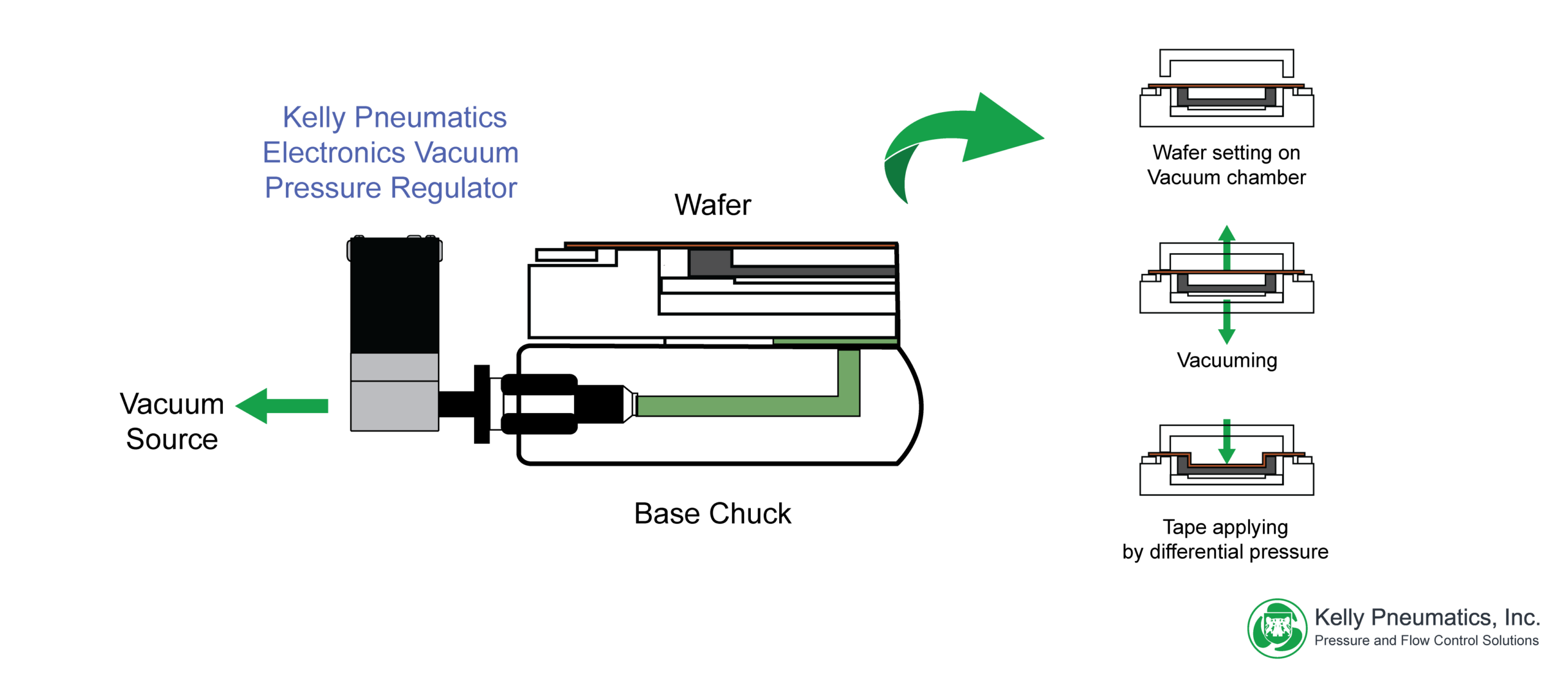
Using the Kelly Electronic Pressure Regulator In The Wafer Dicing process
The Kelly Low Flow Regulator is an excellent solution for using precision pressure control to pilot operate the pressure applied to the wafer during the Dicing process.
An EPR is a device that controls the pressure of a fluid in a system, in this case, the vacuum pressure for the wafer chuck. By maintaining a constant vacuum pressure, the wafer is held securely during the cutting process. This stability is essential for achieving clean, precise cuts on the wafer without the risk of damaging the valuable material.
However, not all EPRs are created equal. Different models and brands offer varying degrees of precision and reliability. For the exacting requirements of semiconductor wafer cutting, a high-quality, reliable EPR is indispensable.